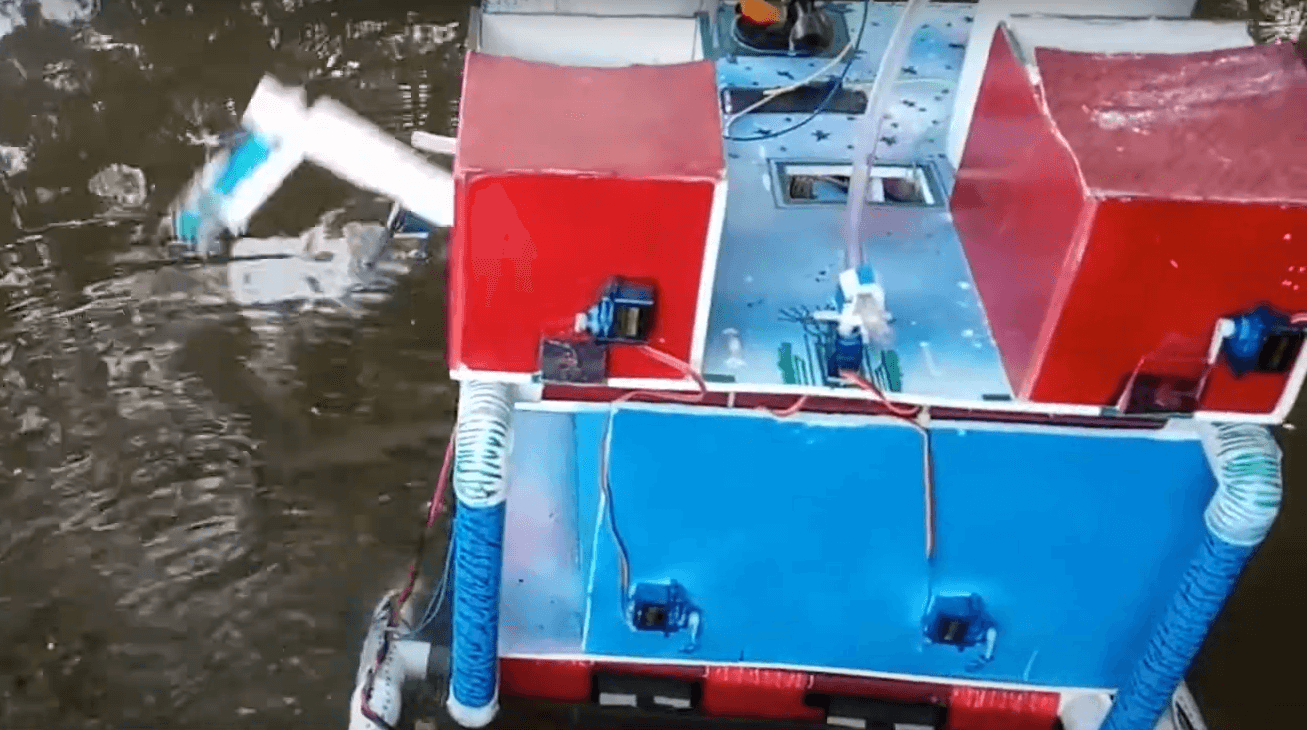
PROJECT OVERVIEW:
When I was a child, I witnessed the plight of people devastated by floods when visiting my grandparents in a small village near the borders. Most of them relied on farming, so they were subjected to the harshest of nature. Even during the summer, the region lacked farming machineries to utilize the fertile soil and meet the growing food demand in the locality. People were starving to death. These sufferings of the people really moved me and from then on, I set my mind to devise a sustainable solution.
Approach:
The project’s approach amalgamated my fascination for robotics and an empathetic understanding of the farming community’s plight. Leveraging hands-on experience gained from science fairs and a robotics kit gifted by my late father, I honed my proficiency in electronics, which was crucial in designing AGIRO.
Growing up, I developed a strong interest in robotics. I routinely participated in science fairs, which exposed me to various electronic components. Realizing the infinite possibilities of electronics, I began exploring it by watching videos, reading blogs etc. My father gifted me a robotics kit for my 15th birthday, and that robotics kit meant everything to me after his demise. Till date, no one has been able to separate me from that box full of tiny electronic chips, motors and transistors. At the age of 17, I collaborated with an NGO to develop drones for the delivery of medical supplies to flood-affected areas. Later, I decided to develop a robotic solution for the enhancement of agricultural facets and production, maximizing efficiency in farming for growing food demand in the flood-affected areas. Robotics, unlike any other field, combines a variety of disciplines, such as engineering, mathematics, mechanics and artificial intelligence which enables us to offer long-term and feasible solutions to a variety of problems. Thus, I decided to solve this problem through robotics and developed a robot named “AGIRO”. The most appealing feature of the robot was that it was a completely autonomous robot capable of functioning in a variety of terrains, including land, water, mud, hilly and rocky fields. It is the first robot created by a high school student that is dedicated to the agricultural industry with such versatile features. The robot moves based on LIDAR which allows it to get a 2-dimensional mapping of the area, and it is equipped with a wireless Wifi camera that enables live monitoring from anywhere in the world, as well as remote control of the robot. The robot can detect and regulate the pH of water, deliver fish food into the pond at a predetermined time of day, and autonomously distribute seeds in a row at specific depth. The reason why it is attractive to the farmers is that the robot is easy to use and its features are customizable according to the needs of the farmer.
- Robot Programming - Raspberry Pi
- Sensor Integration and Calibration
- Computer Aided Design (CAD) - 3D Modeling
Key TECHNICAL Features:
- Multi-Terrain Functionality: AGIRO is designed with high-torque, all-terrain motors and a robust chassis that can handle diverse terrains, including land, water, mud, and rocky fields. This feature equips the robot to perform farming operations under various conditions with ease.
- LIDAR based Intelligent Movement: The robot is equipped with Light Detection and Ranging (LIDAR) sensors, which provide a 2-dimensional mapping of the area. The LIDAR system aids in obstacle detection and avoidance, allowing AGIRO to navigate autonomously within a farming plot.
- Remote Monitoring and Control: AGIRO is integrated with a Wi-Fi camera module for live monitoring. The data is streamed in real-time over an Internet connection, enabling farmers to remotely oversee operations. Moreover, this feature facilitates remote control of the robot, further enhancing operational convenience.
- Customizable Functions: AGIRO is programmed to autonomously execute a range of farming tasks:
- Water pH Regulation: AGIRO is fitted with pH sensors to monitor and regulate water pH levels in farming ponds, critical for optimal aquatic life growth.
- Timed Fish Feeding: An in-built dispenser, guided by a pre-set schedule, automates fish food distribution.
- Seed Sowing: The robot can scatter seeds in defined rows and at specific depths using an automatic seed disperser. This feature is designed considering seed germination needs for various crops.
- Manual Controlled Robotic Arm: A 6-DOF (Degrees Of Freedom) robotic arm grants AGIRO the ability to perform complex tasks such as gripping, lifting, and precise placement of farming tools or products. Manual control ensures flexibility and precision for these tasks.
- Soil Moisture Test and Irrigation: The robot is fitted with soil moisture sensors. Based on the sensor data, the robot can trigger an irrigation system to maintain optimal soil moisture conditions for different crops.
- Automatic Fertilizer and Insecticide Spray: Equipped with a spray system, AGIRO can evenly distribute fertilizers and insecticides across a farming plot. This feature not only optimizes the use of these substances but also eliminates the potential risks associated with manual handling.
- Season-Based Crop Advisor: By integrating weather and crop data, AGIRO can provide suggestions for the most suitable crops to plant in a given season, aiding in improved crop yield.
- Cleaning Water Surface Garbage: With the help of its robotic arm and its ability to navigate water bodies, AGIRO can assist in maintaining cleaner farming ponds by removing surface garbage.
- Ploughing: AGIRO is equipped with a ploughing tool and is capable of tilling the soil, preparing it for the planting season.
KEY TECHNICAL DETAILS:
Microcontroller: Arduino Mega 2560
Prototype Production Cost: ~120 USD
Commercial Production Cost: ~700 USD
Weight: 8 pounds approx.
Dimensions: 30 x 11 x 22 inches
CHALLENGES:
Creating a robot versatile enough to handle different terrains and tasks was a daunting challenge. Balancing AGIRO’s weight for optimal mobility and stability in water, mud, and land required rigorous testing and reiterations. Additionally, integrating and calibrating multiple sensors for accurate functionality was a complex task. I overcame these obstacles by leveraging my skills in robotics, sensor technology, and programming, coupled with a relentless problem-solving mindset.
Project Impact:
AGIRO is not only a testament to my proficiency in robotics but also a reflection of my commitment to leveraging technology for societal good. The robot signifies a promising breakthrough in the agricultural sector, offering efficient, autonomous, and cost-effective farming solutions that can potentially transform rural farming communities.